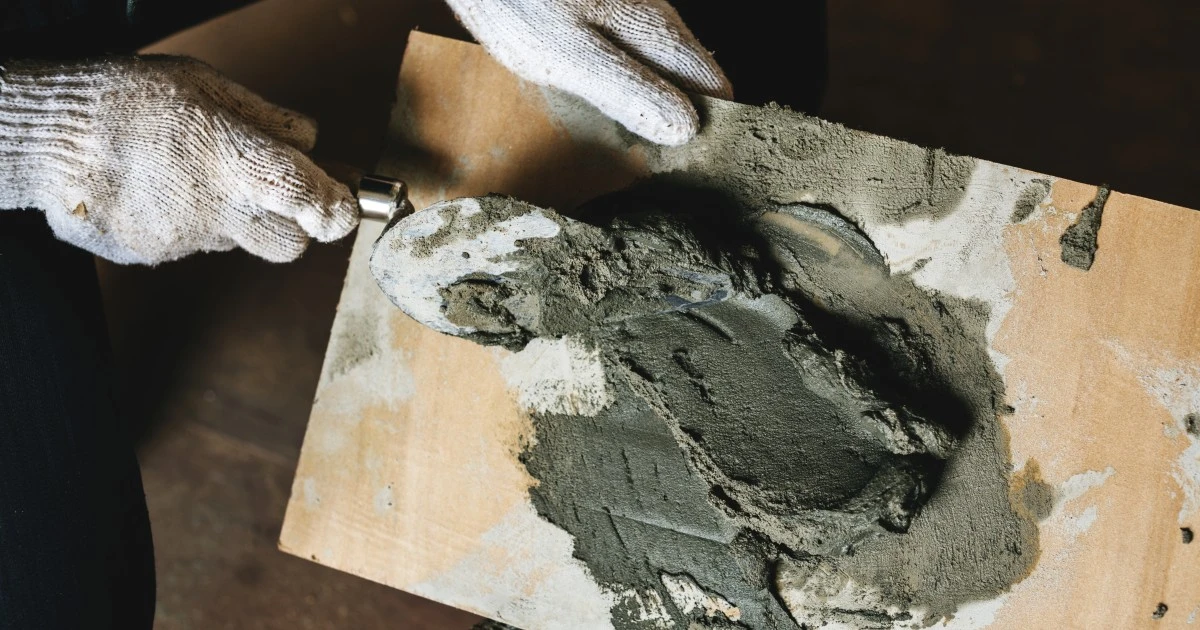
Cement prices in Zimbabwe have surged dramatically over the past two months, rising by up to 100% and causing major headaches for the country's construction sector. A 50kg bag of cement now costs around US$20, double the US$9-10 price just 8 weeks ago.
This price spike can be attributed to a perfect storm of factors - reduced local production, expiring import licenses leading to fewer imports, and booming construction sector demand. With cement being such a vital input for housing and infrastructure projects, the price surge has sparked fears that many developments could grind to a halt if the situation isn't resolved.
Local cement manufacturers have been producing less than usual, with factories undergoing maintenance and retooling to boost production capacity. The government had been providing some relief by issuing special import licenses to cement firms, allowing them to import cement to cover the shortfall cheaply. But with many of these licenses expiring recently, imports have dropped, squeezing supply.
A construction boom across Zimbabwe has fueled record cement demand. Private and public housing projects, new shopping malls and office blocks, road building programs and other infrastructure projects have all required vast cement supplies over the past year. With local production limited and imports down, this has created a perfect storm for price rises.
Some opportunistic retailers have hiked their cement prices to as much as $22 per 50kg bag, as desperate construction firms and property developers scramble to secure dwindling supplies regardless of the costs. Many small hardware stores are also buying cement via intermediaries, paying hefty premiums, as they cannot access stock directly from the manufacturers.
The government has taken some steps to remedy the situation and aid the struggling construction sector. New cement import licenses are being issued to boost supply, and talks are underway with local manufacturers to find solutions. But some industry experts feel this isn't enough.
More radical ideas like temporary cement price controls and currency adjustments to make imports cheaper have been suggested. Others argue ramping up local production should be the priority, regardless of costs, to end reliance on imports.
For Zimbabwe's property industry, the cement shortage comes at a difficult time. The past year saw a boom in residential building across the country, with major new housing developments in Harare, Bulawayo and other cities. Commercial property has also performed well, with new shopping malls, offices and mixed-use buildings popping up to meet demand.
But with cement prices doubling, many projects face major delays unless the situation improves. Small scale home builders and DIY renovators have also been affected, with many retailers unable to source adequate supplies.
Some analysts predict the price rises could last 6 months, especially if import licenses aren't extended and local production remains low. This could see construction slow dramatically, and force many developers and property firms to put projects on hold.
Others are more optimistic, believing prices should stabilize within 8-12 weeks as government interventions kick in. But much depends on how quickly imports can be boosted and local manufacturing output increased.
For major housing projects and apartment blocks already underway, the price spike has been especially problematic. With foundations laid and structures partially built, these developments can't simply halt and wait out the shortage. Many contractors and developers have been forced to pay the higher prices, eating into slim profit margins.
Going forward, closer cooperation between government and private industry will be essential to tackle the shortage. More incentives may be needed to ramp up manufacturing capacity. And ensuring a steady flow of imported cement is crucial until local production meets demand.
Implementing price controls or currency adjustments could also alleviate pressures if done judiciously. And bulk buying schemes, where major developers club together to negotiate import deals, may help large projects source adequate supplies.
The dream of affordable homes for Zimbabwe's citizens relies on a steady supply of fairly priced cement. While the current shortage won't last forever, greater planning and foresight is needed to avoid similar situations down the track. Developing more sustainable local manufacturing capacity and diversity of import sources will be key.
The property industry remains optimistic that, despite some hiccups, Zimbabwe’s construction and housing boom will continue. But keeping cement supply flowing and affordable will require proactive efforts from all stakeholders. With collaborative long-term planning, the current cement price headaches can be overcome, and Zimbabwe’s property development ambitions kept on track.